ExxtendTM technology for advanced recycling and the role mass balance attribution can play in supporting a more circular economy for plastics
Certified-circular polymers can help to drive the demand for using plastic waste as a valuable feedstock
Plastics benefit society in many ways. Because they are lightweight, versatile, and durable, they are the material of choice when compared with alternatives such as paper, aluminum, or glass, and will play a vital role in a net-zero future through enabling new lower-carbon technologies. The challenge society faces is maintaining the benefits of plastics while addressing the issue of waste.
Plastic recycling rates remain low. According to a 2022 report by the Organization for Economic Cooperation and Development (OECD), globally, the bulk of plastic waste ends up “in landfill, incinerated or leaking into the environment, and only 9 percent successfully recycled.”1 While mechanical recycling provides a successful recycling outlet for certain types of plastics, this technology is not able to address all of society’s recycling needs. As global demand for products with lower lifecycle environmental impacts has expanded, so has the value of plastic waste - offering new incentives for the marketplace to support a circular economy. Advanced recycling complements mechanical recycling and supports a more circular economy by driving demand for plastic waste as a valuable feedstock.
ExxonMobil’s Exxtend™ technology for advanced recycling helps address a broader range of plastic waste.
Through mechanical recycling, used plastics are chopped into smaller pieces and melted down to form a limited range of new products. Instead, ExxonMobil’s advanced recycling uses heat to transform plastic waste at a molecular level into raw materials for use in manufacturing a wide array of new products. This process takes place in a unit in our integrated facility and is often referred to as pyrolysis.
Attribution of plastic waste feedstocks
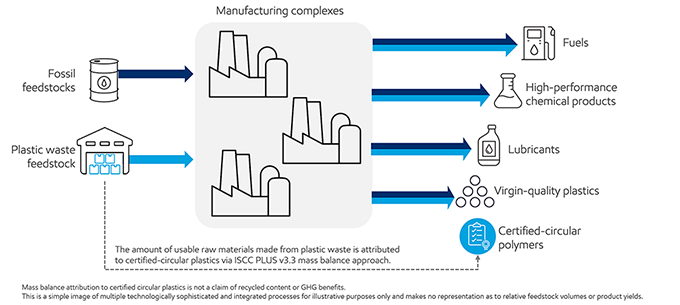
- for every ton of certified-circular polymers we sell, more than a ton of plastic waste avoids ending up in other end-of-life dispositions (e.g., landfill, incineration); and
- for every ton of plastic waste we process, society reduces the need to process approximately one ton of fossil-derived feedstocks.2
“Green power” analogy
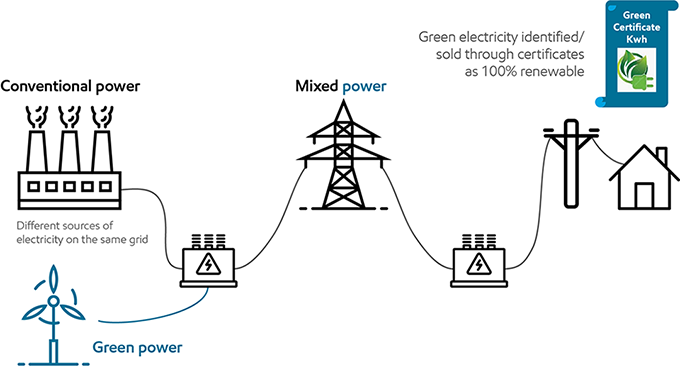
When a residential consumer subscribes to a 100 percent green power service, the electricity they receive may contain a blend from renewable and non-renewable sources. However, the crucial point is that the amount of electricity they purchase matches the amount of renewable energy put into the grid by those solar and wind farms. In other words, the renewable energy generated has been “attributed” to their green power purchase. By choosing this service, they increase the demand for renewable energy, reduce the need for fossil-based power generation, and contribute to the growth of the renewable energy sector.
Likewise, in advanced recycling, customers also pay a premium to receive a certificate of circularity that matches the volume of their purchase to a corresponding amount of plastic waste that was transformed back into raw materials. Similar to the green power analogy, in this context, the amount of useable raw materials processed from the plastic waste in our refinery is freely attributed to the plastic sold as “certified-circular plastics.” The certificate we provide our customers is not a claim that our certified-circular polymers contain any “recycled content.”
Rather, the certificate represents an assurance that we followed a robust mass balance attribution system that is certified by a third-party on a feedstock basis. Our advanced recycling facilities and process are certified via an independent, third party certification system called International Sustainability and Carbon Certification (ISCC) PLUS. ISCC “has been developed through an open multi-stakeholder process and is governed by an association with more than 250 members, including research institutes and NGOs.” 3
Modern refineries and chemical plants contain many technologically sophisticated processes that are integrated across multiple manufacturing steps. These complex processes represent decades of industry innovation and investment and provide significant benefits to society by enabling a wide range of raw materials to be efficiently, economically and safely converted into hundreds of products critical to modern life. Mass balance methodology, such as that employed by the ISCC PLUS certification system, sorts through this complexity by drawing a box around the entire system and looking at the balance of inputs and outputs of the entire system. Mass balance methodology quantifies the value of substituting fossil-derived raw materials with more-circular raw materials and attributing the beneficial impact to the products produced from the complex system. For example, in accordance with the mandatory provisions of the ISCC PLUS methodology, recyclers/manufacturers attribute the usable raw materials that are produced from plastic waste to the streams that can be used for polymer production, but only up to the physical size of those streams that flow within the system. The integrity of the ISCC PLUS certification is built on these and other auditable boundary conditions.
- diverting plastic waste from landfills and incineration into useful raw materials;
- monetizing plastic waste to drive better collection and sortation;
- supporting an alternative to fossil-based feedstocks;
- increasing the range of plastic products that can be recycled;
- contributing to the growth of the advanced recycling sector;
- propelling the increase of plastic recycling rates; and
- delivering new, certified-circular products into important end uses such as food contact and medical supply.
2 On a global, macroeconomic basis, assuming constant demand
3 https://www.iscc-system.org/