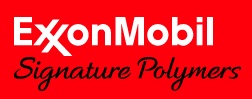
All our polymers are now positioned under a single portfolio brand: Signature Polymers. We will be making these modifications over the next six months so you will see both old and new grade names highlighted moving forward.

Bags and sacks
Applications and benefits
Typical applications include films for medium- and heavy-duty bags and sacks (laminated or nonlaminated) that package products like rice, cereals, animal foods, lawn and garden produce, fertilizers and resins.
Across the supply chain, performance PE polymer -based solutions deliver performance and value. Formulations can be tailored to derive maximum benefit in both vertical and tubular form as well as fill and seal (FFS) processes.
- High film output, excellent cost performance balance, easily adapted formulations
- High packaging-line speeds, excellent product imagery/branding potential, cost optimization opportunities, rigidity and stiffness for good machinability
- Superior transportation and storage packaging integrity, excellent product imagery/branding potential, good creep resistance during storage
- More convenience and less spillage for consumers
Compared with conventional alternatives, performance PE polymer -based films in bags and sacks for pet foods, lawn and garden products, rice and other products offer:
- Improved film extrusion with potential film-line output benefits
- Simplified product formulation, reduced costs, improved film quality and consistency
- Lower working capital through material savings and lower inventory
- Tailored tensile and modulus properties, reducing bag deformation through improved creep
Performance polymers improve the overall production quality of polypropylene (PP) raffia tape by enhancing the two properties critical in manufacturing: elongation and tenacity. Because tapes have higher tenacity, they can be stretched further and there is less tape breakage. Performance polymer-based AFMB (anti-fibrillating masterbatch) helps improve the elongation of the tape and allows an increased dosage of AFMB for noncritical applications, thus reducing the cost of the fabric.
- Improved tenacity
- Higher elongation
- Less tape breakage with higher filler loading
- Faster line speeds and improved output
- Downgauging opportunities
- Cost-reduction opportunities
Manufacturers of polypropylene (PP) woven sacks look for lower costs through seal extrusion rather than stitching PP woven sacks, stronger sacks, higher throughput and cost reduction opportunities. Adding performance polymers to a conventional PP formulation can deliver:
- Opportunities to tailor the coating properties to meet the requirements of end-use applications by blending with PP and polyethylene (PE)
- Effective seals at very low temperatures (below conventional polymers), increasing line throughput
- Low material consumption by using blends, coextrusion and downgauging
- High bond strength for robust packaging solutions – better than homopolymer polypropylene (hPP) and random copolymer polypropylene (RCP)
- Excellent adhesion without pretreatment on woven sacks
- High UV resistance compared with hPP
- Controlled coefficient of friction (COF) for effective pallet stability
- Ease of processing on conventional extrusion coating line
Product solutions
-
Creating heavy duty sacks with sustainability benefits: The value chain working together.
See how Selene, ExxonMobil, W&H and Aventus worked together to develop, create, test and fill heavy duty sacks with films containing 50% post-consumer recycled (PCR) PE content using ExxonMobil’s Exceed™ XP 8318 and Exceed™ 1012 performance polyethylene resins. Learn what each company contributed and evaluate the results.
Featured resources
View highlighted news, events, technical papers and case studies below. To see our full collection of resources, browse our Library.-
Stronger heavy duty sacks using eXtreme Performance films
ExxonMobil's Exceed™ XP performance polymers provide a range of benefits that allow the fabrication of high-quality 3-layer heavy duty sack films. High package integrity, excellent sealing characteristics, enhanced machinability and outstanding operational efficiencies are all possible.