Shale gas production offers opportunities and challenges
The opportunity: growing shale gas production
U.S. natural gas production is projected to grow nearly 4% annually until 2020 and approximately 1% annually between 2020 and 2040. This is the result of the continued development of shale gas and tight oil plays which will account for nearly two-thirds of natural gas production by 20401. The growing availability of natural gas is an opportunity for the ethylene industry, as it has led to lower cost feedstocks for gas cracking and thus the addition of new gas cracking capacity.
1U.S. Energy Information Administration | Annual Energy Outlook 2017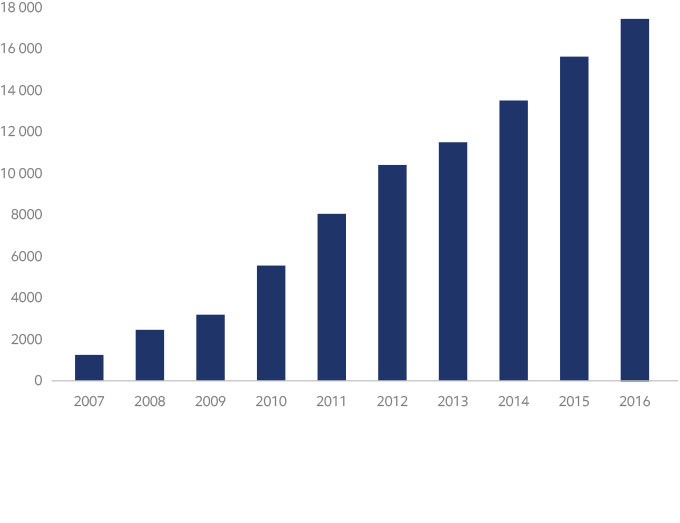
The challenge: increased compressor fouling
The relatively low ethane price relative to the prices of oil-based naphtha and gasoil feedstock have resulted in a relatively higher ethane feedstock in the North American ethylene production2.
2 U.S. Energy Information Administration | Annual Energy Outlook 2015
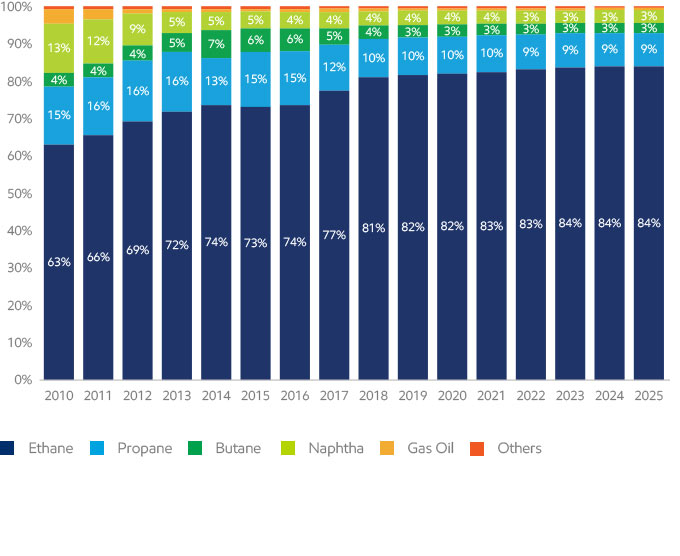
With the recent shift toward lighter ethylene cracking feeds in North America, fouling problems have increased. Gas crackers specifically face fouling issues due to the low volume of heavier aromatic fluids formed during cracking. Furthermore, increased ethylene production from ethane has led to fewer internal heavy streams available for use as a wash oil.
As fouling occurs, the compressor’s flow is restricted, resulting in increasing frictional pressure drop. Leading to disrupted pressure and distribution profiles and increased temperature, power requirements and suction pressure. In the end your gas compressor’s yield and capacity will decline. Heavy aromatic fluids have a proven track record as effective compressor wash oils but have at times faced supply and availability challenges.
The result: increasing demand for wash oils
Increased capacity has resulted in rising demand for compressor wash oil. Furthermore the transition of some naphtha (liquid) crackers to gas feedstocks has further grown demand for compressor wash oil. With this transition less internal streams are available for use as compressor wash oil. Current products used for compressor wash oil are generally C10-C12+ aromatic based.
ExxonMobil Exx-Wash™ can meet your requirements for efficient compressor cleaning
Key benefits and specs of Exx-Wash compressor wash oil
ExxonMobil Product Solutions has a solution that can meet your needs: Exx-Wash, a portfolio of tailored injection wash oils to maintain cleaning efficiency.
Overview of products and typical values
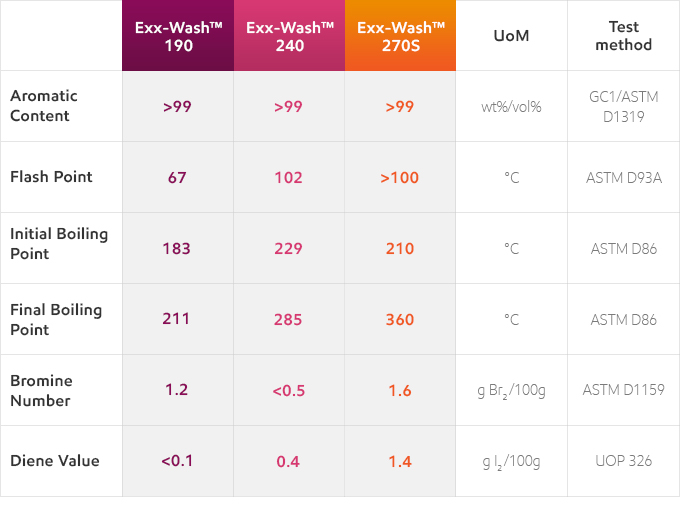
Notes:
Typical values indicated in this chart describe typical physical properties and do not constitute specification limits. The typical value may vary over time.
Test methods are available on request and consistent with sales specifications.
Exx-Wash compressor wash oil is specifically designed to deliver an array of benefits for olefins manufacturers:
- Offers efficient cleaning due to strong solvency
- Provides two grades each with a distinct and narrow boiling range to accommodate your specific operating conditions
- Minimizes corrosion and fouling due to very low sulfur levels and low “heavies” content
- Delivers consistent quality for process gas compressor operability and reliability optimization
What are the properties of an efficient compressor wash oil?
The key properties of an efficient and effective compressor wash oil are strong solvency, excellent volatility in the desired distillation range and fluids purity. Discover how Exx-Wash performs by selecting the property of your choice.
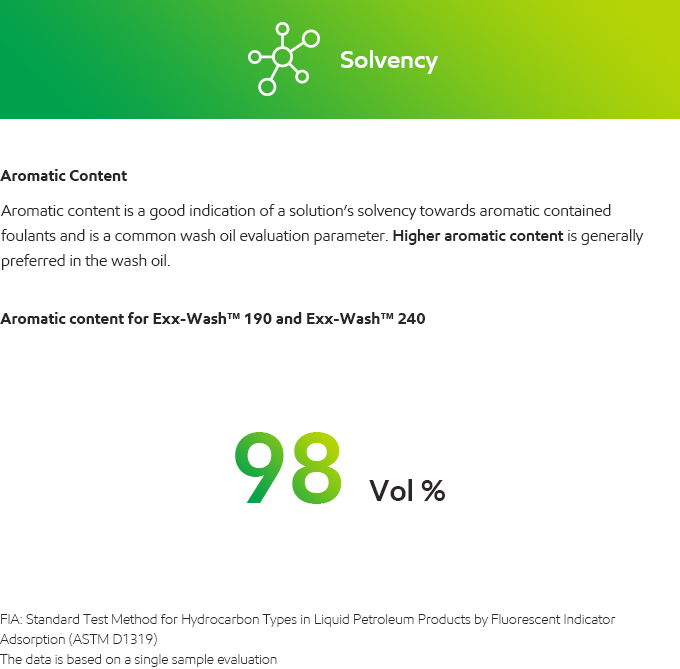
Keep your business in motion with Exx-Wash™
How do you improve compressor efficiency with Exx‑Wash?
ExxonMobil Product Solutions' Exx-Wash process oil portfolio is specifically designed to deliver an array of benefits for olefins manufacturers.
Minimum emulsion
Density delta increases with increasing temperature. A density comparison: Exx-Wash™ 240 vs. water:
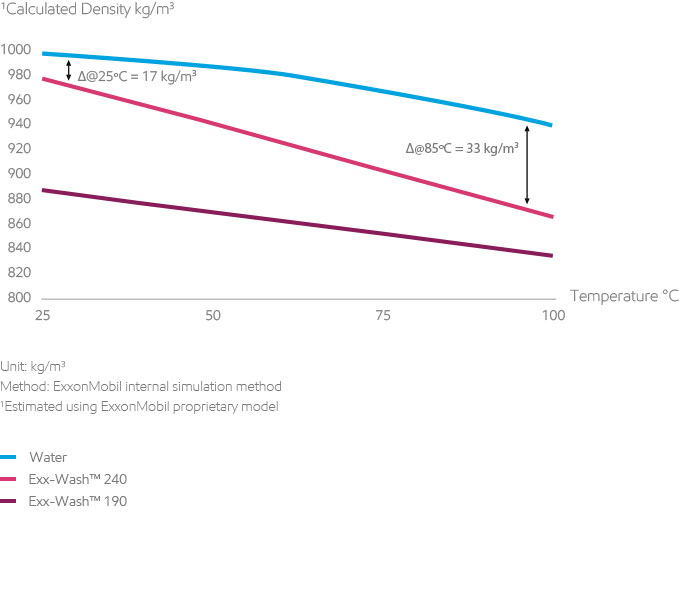
It’s so good – we use Exx-Wash™ in our own operations
We stand by the quality of our own products and use Exx-Wash™ 240 in our ethylene compressor operations on a daily basis. Our engineers have this to say about the product:
“By switching to Exx-Wash™ 240 ExxonMobil Product Solutions realized improvement to ethylene compressor operations in the stabilization of the compressor efficiency.”
ExxonMobil, Basic ChemicalsSelect the operating condition that best represents your gas process compressor and discover the maximum temperature at constant pressure, or the minimum pressure at constant temperature. This is visualized in the graph below: above the product line, the Exx-Wash wash oil is expected to be liquid, below it is expect to be in the gas phase.
How to interpret your results
Product performance is best when the stage points are above the pressure/temperature curves. This gives an indication that the Exx-Wash compressor wash oil is expected to remain liquid upon injection or under ideal conditions.
Operating Condition
Temperature (°F) | Pressure (psig) | Pressure (psia) | |
---|---|---|---|
Stage Point Input 1 | 14.7 | ||
Stage Point Input 2 | 14.7 |